切削加工の分野において工作機械や切削工具は目覚ましい進化を遂げていますが、石油由来の切削油数百リッターをKW単位の電力を長時間消費しながら高圧のポンプで循環させ、劣化して切削性能が落ちると産業廃棄物として処理するといった環境負荷の大きい方式自体は古くから変わっていません。しかも切削性を高めるために成分調整された数百リッター切削油の大半は切削に使われることなく切屑を流すために循環しています。切削加工においてはCO2排出量の大半をこの切削油に関することで占めていますので、この当たり前のやり方に疑問を持つことが技術革新に最も重要なことです。
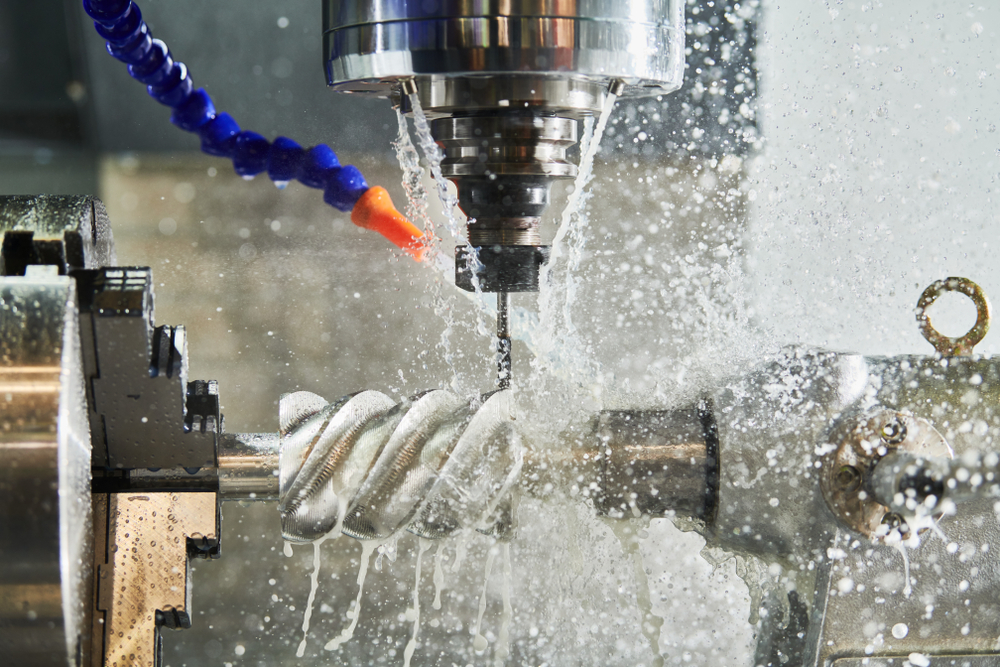
ケイエステックはミスト加工を活用すればその常識を覆せると真面目に考えています。切削油を使用する目的として加工補助(潤滑・冷却・抗溶着)と切屑処理に分けられますが、切屑処理の方には高性能な切削油は必要はなくまたポンプ圧も切屑が流れる程度で十分です。つまり加工補助の部分をミスト加工に置き換えできれば、加工補助に使用する少量の部分だけ高性能な(CO2排出量の多い)切削油を使用し、使用量の多い切屑処理には2~3%程度の防錆・防腐添加剤をいれた水(CO2排出量の少ない)でよくなります。またロボットやローダーではなく作業者がワークチェンジする場合はエアブローで切屑処理できるためクーラントポンプ自体を廃止することもできます。
「ミスト加工なんてしょせんクーラントポンプのない設備でドライで加工するよりはましといった程度のもの」といった認識の方も多いと思います。しかしMQL(油性ミスト)はミスト加工として初めてクーラントポンプよりも効果が高いという用途を確立し、切削加工の分野で確固たる地位を得ました。それでも切削加工全体からすればほんの一部です。しかしミスト加工はMQLだけではありません。以下でミスト加工の現状と可能性について詳しくご説明したいと思います。
【目次】
ミストの種類
ミスト加工とは圧縮空気を用いて霧状にした切削油を切削点にピンポイントで供給し加工を行う技術です。セミドライ加工とも呼ばれています。ミスト加工には主に以下の3種類があります。
① 油性ミスト
不水溶性切削油(植物油・合成エステルなど)を毎時10~100cc程度噴射します。一般的にMQLと呼ばれ、ミスト加工といえばこれのことと認識しているユーザーも多くいます。わずかな消費量でも効率よく潤滑効果を与えることができますが、水分を含まず冷却効果が低いため発熱量の大きい加工には不向きです。
➁ 水溶性ミスト
水溶性切削油(エマルジョンやソリュブルなど)を毎時200~1000cc程度噴射します。冷却効果が高く発熱量の大きい加工にも対応できますが、潤滑効果では油性ミストに劣ります。
➂ 2液ミスト
①と➁を組み合わせた方法です。通常のクーラントポンプで使用する場合は油性と水溶性をタンク内で混ぜるわけにはいきませんのでどちらか一方しか選択できませんが、ミスト加工の場合は切削油を循環利用しませんので組み合わせて使用することで両方の特性を活かした加工ができます。
名称としてはミスト加工・セミドライ加工は①~➂を含むすべて、MQLは①だけのことという感じです。それに対して通常のクーラントポンプによる加工はウェット加工と呼ばれます。
ミスト噴射方法(外部給油・内部給油)
工作機械に取付けてミストを噴射する方法には以下の2つの方式があります。
①外部給油方式
切削工具の刃先に設けられたオイルホールからではなく、外部ノズルから切削点に噴射する方法です。クーラントポンプの場合はノズルから出た切削油が周辺に広がりますが、ミストはピンポイントで噴射位置が固定化されるため工具によって加工位置が変わる自動工具交換(ATC)の工作機械には不向きです。またロングドリルのように穴の奥を加工する工具ではミストが届かないため使用できません。外部給油式の特徴として切削油をミスト化させることが容易にできるめ、シンプルで安価な装置でも使用できます。
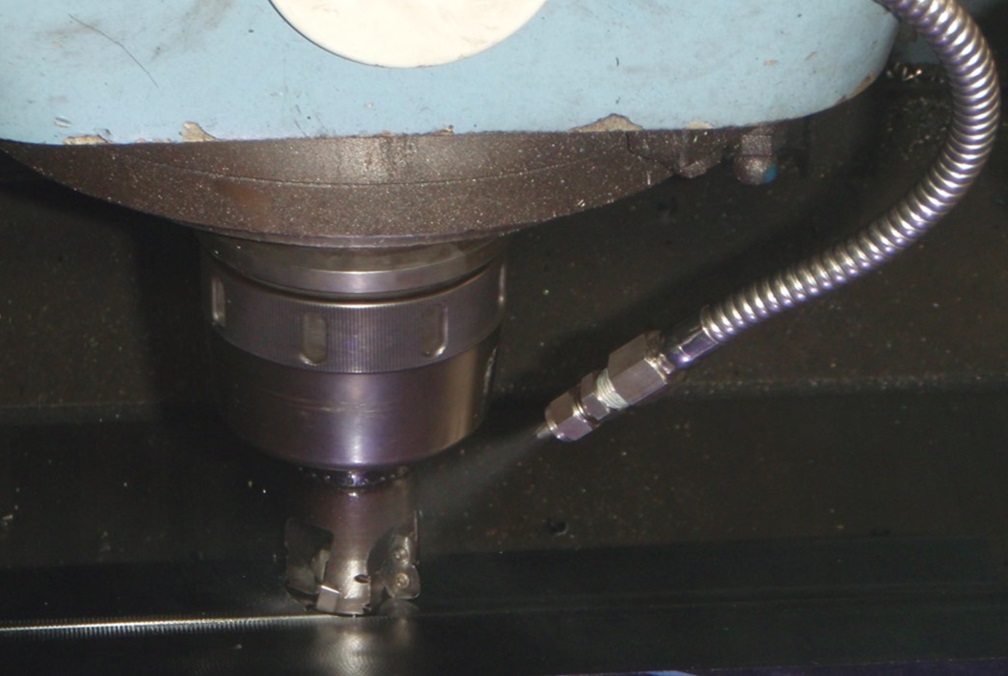
➁内部給油方式
工作機械の内部配管を経由し工具自体に設けられたオイルホールからミスト噴射する方法です。マシニングセンターのスピンドルスルーやNC旋盤のタレットスルーがそれにあたります。各工具の切削点に向けてミスト噴射できるため様々な工具や量産部品の加工に対応できます。また外部給油に比べてミスト出口から切削点までの距離が近いため、切削油のロスが少なく加工性能もアップします。一方で配管経路が複雑で距離も長くなるため、オイルホールから瞬時にミスト噴射させるには内部給油専用の装置が必要となります。
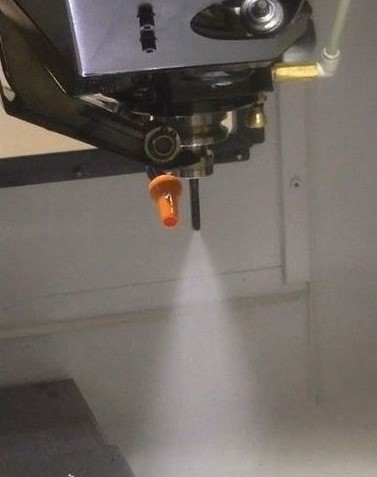
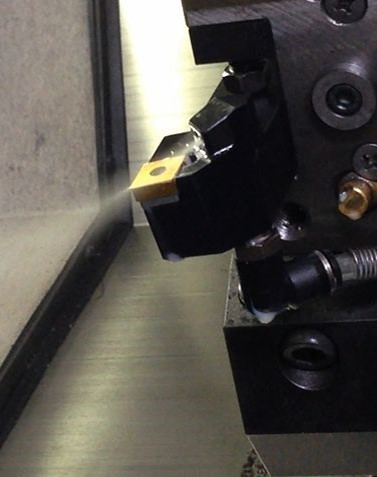
汎用工作機械で使用されるミスト器具
マシニングセンターやNC旋盤といったNC工作機械の場合、通常は切削油をクーラントタンクからポンプで汲み上げ加工ワークに大量に噴射しそれを循環して使用するウェット加工です。一方で汎用工作機械(ボール盤・汎用旋盤・フライス盤など)のようにクーラントタンクやポンプを備えていない設備は基本ドライ加工します。しかし汎用工作機械でも加工内容によってはドライで加工することが難しい場合があります。そんな時にマグネットで噴射ノズルを簡単に後付けできて周囲に液が飛び散らない外部給油式のミスト器具(ルブリケーターや点滴)をクーラントポンプの代わりとして使用されてきました。加工内容に合わせて油性ミストと水溶性ミストを使い分けることができます。
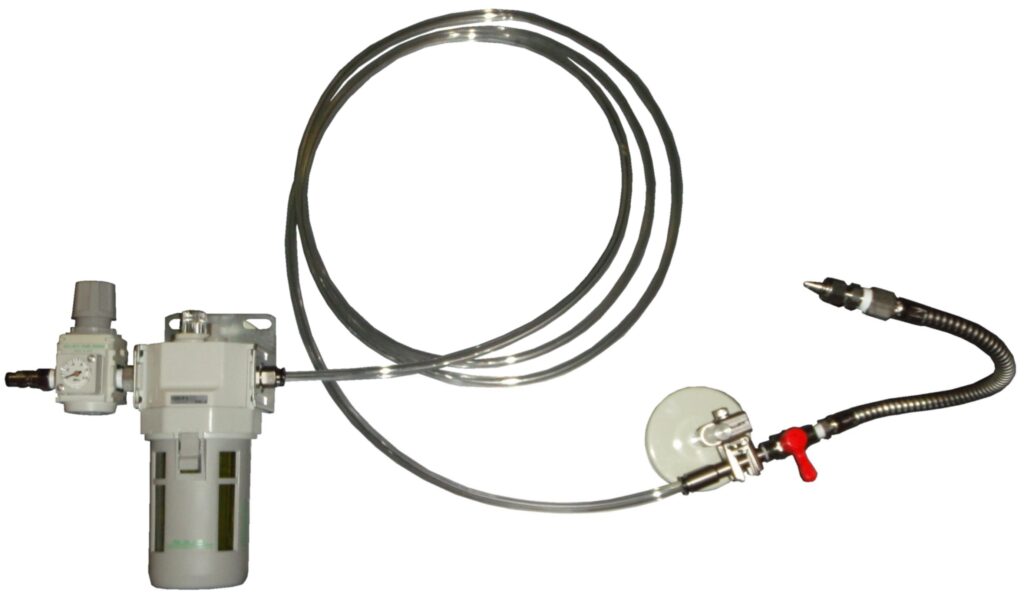
環境技術としてのミスト加工
ミスト器具はあくまでもクーラントポンプが使えない機械で簡易的に使用されるものですが、1990年代から環境技術としてそれまでとは全く違った目的でミスト加工が注目されました。切削加工の分野では環境負荷低減のために切削油の使用量を減らすことが最も効果的ですが、当時自動車メーカーを中心に切削油を一切使用しないドライ切削の実現に取り組んでいました。切削工具に耐熱コーティング処理をするなどが主な手段でしたが、さすがにそれだけでは従来の液体クーラントと同等の工具寿命で加工することができませんでした。そこで次の手段としてできるだけドライに近い最低限の潤滑油(Minimun Quantity Lubrication)をミストにして加工点に供給するMQL(油性ミスト)が大々的に検討されることになりなりました。MQL装置はそれまでの汎用工作機械で使用される簡易的な手動操作のミスト器具とは違い、自動車部品などを加工するNC工作機械用としてプログラムによる自動運転に対応し、内部給油方式でミスト噴射できる高性能なものでした。ウェット加工と比べてミスト加工が環境に良いとされる理由は以下になります。
- 切削油の使用量を大幅に削減できる
- クーラントポンプのように大きな電力を消費しない
- 切削油を循環使用しない(使い切り)ため廃液(産業廃棄物)が発生しない
環境技術として期待されたMQLは様々な用途でウェット加工と比較されその効果を検証さましたが、当初の目的であった切削油の使用量を大幅に削減させるという面では十分な結果を残したとはいえませんでした。その主な要因としては次の2点があげられます。
- MQL(油性ミスト)はウェット加工に比べて冷却効果が低く、溶着が発生するアルミ材の加工や発熱量の大きい加工には対応できなかった。
- ミストでは機内に堆積した切屑を洗い流すことができなかった。
完全ドライ切削も含めた当時の取り組みの結論は、「耐熱コーティング等によって切削工具の性能が上がりドライやMQLである程度加工できたとしても、ウェット加工による冷却効果を加えた方がより耐久性は上がるのでコスト面を考慮すると冷却効果の低いドライやMQLが液体クーラントに取って代わることは難しい」ということでした。結果的にウェット加工は現在も切削加工機の大半で使用されています。
MQLが採用された用途
環境負荷軽減という目的では十分な成果をあげたとはいえないMQLですが、ある特定の加工では液体クーラントよりも工具寿命が延びるという評価を得て、その用途では標準的に使用されるようになりました。特に有名な用途は以下の2つです。
- SC材の小径ロングドリル深穴加工(代表例:クランクシャフトの油穴)
- 小径ボールエンドミル加工(代表例:金型の仕上げ)
いずれもウェット加工をすると工具寿命が悪くなり、MQLを使用することで改善された事例です。これらの加工の共通点は小径の工具のため切削時の発熱量が少なく、液体クーラントではむしろ冷やしすぎによる悪影響が出るということです。例えば小径のボールエンドミルは先端のボール形状の一部が接触しているだけですので、加工径が極端に小さく高速回転しても加工部の周速は上がりません。特に超硬工具は切削温度が上がることで材料を軟化させて削りますので、クーラントをかけて切削温度が下がると逆に切削抵抗が高くなってしまいます。そこにMQLの特徴「冷却効果は低いが潤滑効果をピンポイントで切削点に供給する」がうまくマッチしました。ちなみにこれらの用途で使用されるNC工作機械は上記以外の切削工具では液体クーラントが必要になるためMQLとクーラントポンプを併用しているケースがほとんどです。
ミスト加工の普及には内部給油方式に対応すること
もともと汎用工作機械で使用する簡易的なミスト器具から、NC工作機械での量産部品の加工に使用されるようになったMQLの登場はミスト加工の大きな転換点となりました。その最大の特徴はMQL装置が内部給油方式に対応したことです。それまでのミスト器具は単純な外部給油式のものしかありませんでしたが、自動車部品をはじめ切削加工による工業製品の大半がATCを備えたNC工作機械で製造されますので、切削加工全体に普及するためには内部給油方式に対応することが大前提となります。MQL装置は油性切削油を粒径の細かいドライフォグにして空気に浮遊させ、その状態で工作機械の内部配管を搬送するという方法で内部給油を可能にしました。この方法はドライフォグ化する油性切削油では有効ですが、ミスト同士が結合して液化してしまう水溶性切削油には適用できません。
ミスト加工の新たな選択肢である水溶性ミスト
2020年代になり脱炭素を目指して切削加工業界でも新たな取り組みが行われるようになり、アルミ部品の加工に水溶性ミストが検討されるようになりました。自動車の軽量化に伴い自動車部品の多くに使用されるアルミ材の加工は自動車メーカーが取り組むべきメインのターゲットです。アルミ加工の特徴として加工温度が上がると切削工具の刃先に溶着が発生するため冷却が必須であり、それには冷却効果の高い水溶性ミストが良いと考えられたからです。ようやくミスト加工の新たな用途開発が始まりました。水溶性ミストはアルミ加工に限らず水溶性クーラントが使われているほとんどの切削加工に対応できます。現状使用している水溶性切削油をそのままミスト噴射して刃先に供給すればよいからです。
内部給油方式の水溶性ミスト装置
ドライフォグでミスト搬送できない水溶性切削油を内部給油方式で瞬時にミスト噴射するのは非常に困難です。特にマシニングセンターでは高速回転するスピンドルの中を通過する際に液化して遠心力の影響をうけミストが出てくるまで数分かかってしまうこともあります。水溶性ミスト仕様のマシニングセンターを販売している工作機械メーカーもありますが、これは遠心力の影響を受けないミスト専用のスピンドルを備えた特殊仕様の工作機械でその会社の機種でしか使用できません。ケイエステックのエスリムは独自ポンプ技術により、遠心力に負けないように液状の切削油とエアーを瞬時に工具先端まで搬送し、オイルホールから噴射する際に霧化させるという方法で内部給油によるミスト噴射を可能にしました。通常のNC工作機でも油性・水溶性に関わらず瞬時にミスト噴射できるミスト装置で、様々なメーカーや種類の工作機械で使用できます。水溶性ミスト加工に興味が出たので試してみたいといったご要望がありましたらぜひご活用ください。
水溶性ミスト加工の効果
「同じ水溶性切削油を使用したとしてもポンプとミストでは量も威力も違うのでは?」と思われるかもしれません。しかし切屑処理は別として切削点に及ぼす影響だけで考えるとポンプで大量に噴射された切削油の大半は全く切削点に触れることなく流れ落ちており、実際に加工点で使われている量はほんのわずかです。ミストの場合は切削に必要な量だけをピンポイントで加工点に供給しますのでより効率的といえます。さらに液化状態では切削加工時の遠心力の影響を受けますので切削工具の刃先部分には到達しにくくなります。高圧クーラントが使用されるのは遠心力に負けないように圧力で強制的に液体を刃先に押し込むためです。一方で微粒子のミストは遠心力の影響を受けることなく刃先に到達することができます。
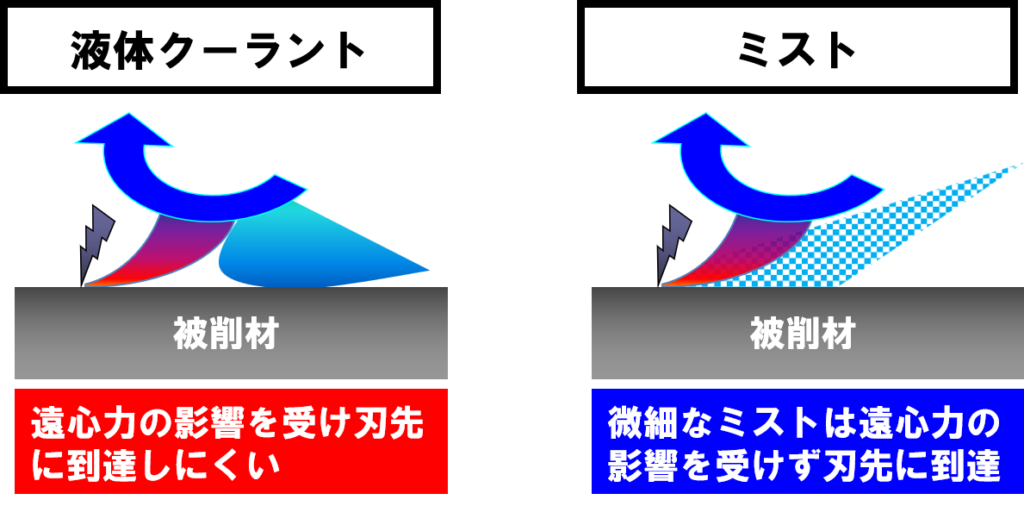
また刃先到達したわずかな水分で切削熱を冷却するためには、水分をいかに効率よく蒸発させ気化熱を利用するかが重要です。水は液体の状態よりも霧化して熱源に触れさせる方が効率よく蒸発させることができます。例えば熱した鉄板の上に水を垂らしても、水滴がしばらく弾けてから蒸発しますが同じ量を霧吹きで吹くと一瞬で蒸発します。このようにクーラントポンプを比べると一見頼りなく思えるミスト加工ですが、切削点に及ぼす効果で見れば決して劣っているわけではありません。
ミスト加工を行う際の注意事項
液体クーラントからミスト加工に切り替える際、工作機械にミスト装置を取り付けるだけではうまく行かないケースがあります。これは工作機械もツーリングもミストで使うことを前提としていないため、そのままの状態で使用するとミストが正常に噴射されないからです。今後ミスト加工が普及してそれに対応した工作機械やツーリングが市販されるようになればよいのですが、それまでは以下の注意事項を確認して個別に対応する必要があります。過去にミスト加工をテストをしたけど工具寿命が悪くなったというケースでは、ミストの効果が無かったからではなく正しくミスト噴射されていなかったからかもしれません。
- ミスト配管経路に漏れがないこと
- ミストが工具の切削する部分全体に必ず当たっていること
- ミスト噴射口(オイルホール)の断面積および総断面積が大きすぎないこと
1. ミスト配管経路に漏れがないこと
ミスト配管経路(工作機械の内部配管・ツーリング内)に漏れがあるとミストの吐出が間欠状態になったり、エアーだけしか出てこなかったりします。MQL(油ミスト)の場合は液量が少なすぎて目視できないので気づきにくいのですが、水溶性ミストの場合は一目瞭然です。漏れが無いようにするのは当たり前と思われるかもしれませんが、通常のクーラントポンプで切削油を出す場合は多少の漏れがあっても使用上問題がないため、実は液が漏れる箇所が結構あります。
- NC旋盤のタレット後部にあるプランジャーとタレットの接触部
- タレットの各ステーションとツーリングホルダーの接触部
- サイドロック式の工具のボルトの隙間
- ホルダーのキャップとシャンクの隙間 など
要は配管経路上の部品と部品の接触部分にはすべてOリング等のシール材が必要ということです。 ミストが正常に噴射されない場合は配管経路上に液漏れが無いか確認してください。これらの対処は面倒に思われかもしれませんが、クーラントポンプの場合でも本来は漏れがあると圧力低下などの無駄が発生しますので必要な対応です。ミスト用というわけではなくてもこのような漏れ対策用のツーリングも市販されています。もちろんミスト加工にも有効です。
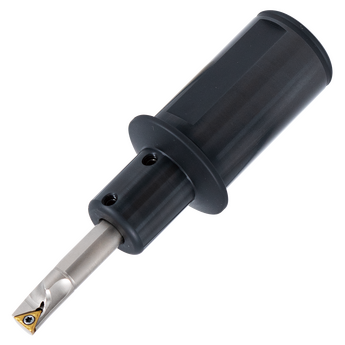
2. ミストが工具の切削する部分全体に必ず当たっていること
工具の切削する部分とは刃先のことですが、市販されている切削工具をそのままミストで使用しても刃先に当たらないケースがあります。クーラントポンプの場合は切削液がオイルホールから噴射された後に周辺に広がっていきますが、ミストの場合オイルホールが向いている方にしかあたりません。以下のような工具が代表例ですが、そういった工具でミスト加工を検討する場合はミストに合ったものを選定するか、ミスト専用の工具を個別に設計する必要があります。
- 太径ドリル(刃先交換タイプ)
- ドリルリーマ
- 段付きドリル
- タップ(先端面にオイルホールがあるタイプ) など
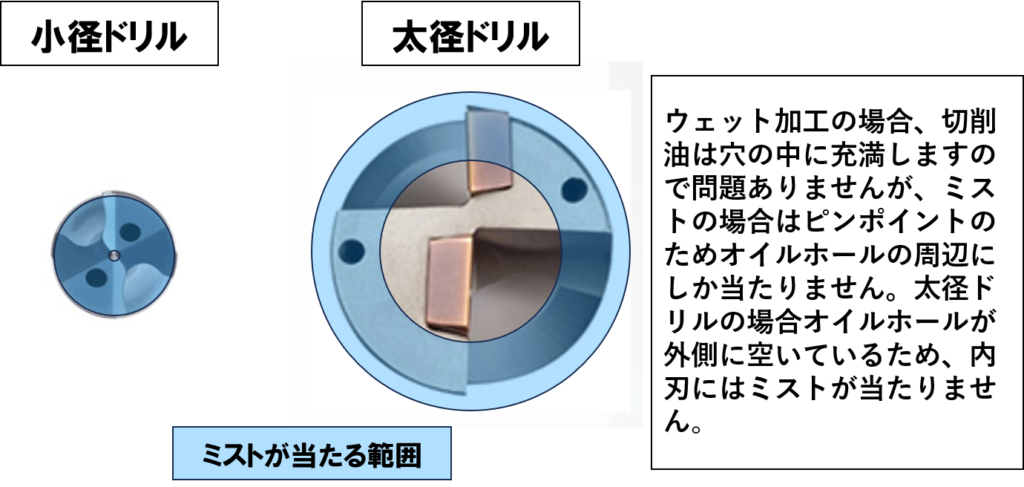
太径ドリルの場合は図のようにドリル径の外側部分にしか当たりませんので、一方のオイルホールを内側(内刃の近く)に変更すればミストでも使用できます。内部給油用のドリルリーマはドリルの先端にしかオイルホールがありませんので、ドリルの刃にはミストが当たりますが、リーマの刃(側面)には当たりません。段付きドリルやタップも同様です。これらの工具はミスト専用に側面に当たるようにオイルホールの追加する必要があります。このようなミスト専用設計が必要な切削工具は現状特殊対応となるため納期やコスト面を考慮するとすぐにミスト化させることは困難ですが、まず既存の工具でもミストで使える加工仕事からミスト加工が普及していけば、いずれ切削工具メーカーもミスト専用工具を標準品として販売して頂けるようになると思います。
3. ミスト噴射口(オイルホール)の径および総断面積が大きすぎないこと
ミストが噴射されるオイルホール径には適正なサイズがあります。特に大きすぎるとミスト粒径が大きくなりすぎて飛沫になったり、無駄にエアーを消費してしまいます。クーラント用のノズルは内径が大きいため注意が必要です。またオイルホールから切削点までの距離が内部給油は近く(数ミリ)、外部給油は遠く(50~200mm)と異なりますので、それに合わせて適正な径も変わります。
【ミストに適したオイルホール径】 内部給油 0.5 ~ 1.0mm 外部給油 1.0 ~ 2.0mm
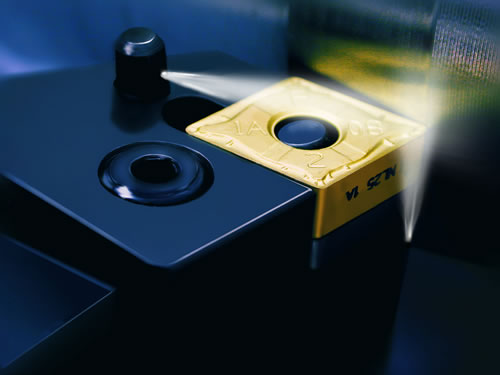
また内部給油用のフライスカッターのようにカッターのチップの数だけオイルホールがあるような工具は、オイルホールの総断面積が大きくなりすぎて、エアー供給量が追い付かず全くミストが噴射されなくなります。ミストが噴射できる許容総断面積(全オイルホール面積の和)は以下になります。
【総断面積】 < 10 ㎟
例) チップ数10枚のフライスカッターの場合
オイルホール径 1mm x 10個 0.5 × 0.5 × 3.14 × 10 = 7.85 ㎟